This sponsored article was created by Insight magazine, the sponsored content division of MHM Publishing, on behalf of International Aviation Composites.
Over 30 years of specializing in helicopter rotor blade repair is not a milestone that many companies can celebrate. But International Aviation Composites — known as IAC — has already surpassed that milestone and achieved several others as it continues to serve established and new customers in 2024.
As one of the few independent helicopter rotor blade repair stations worldwide since 1992, IAC has honed its skills and processes to ensure the efficient and safe inspection and repair of both metal and composite main and tail rotor blades.
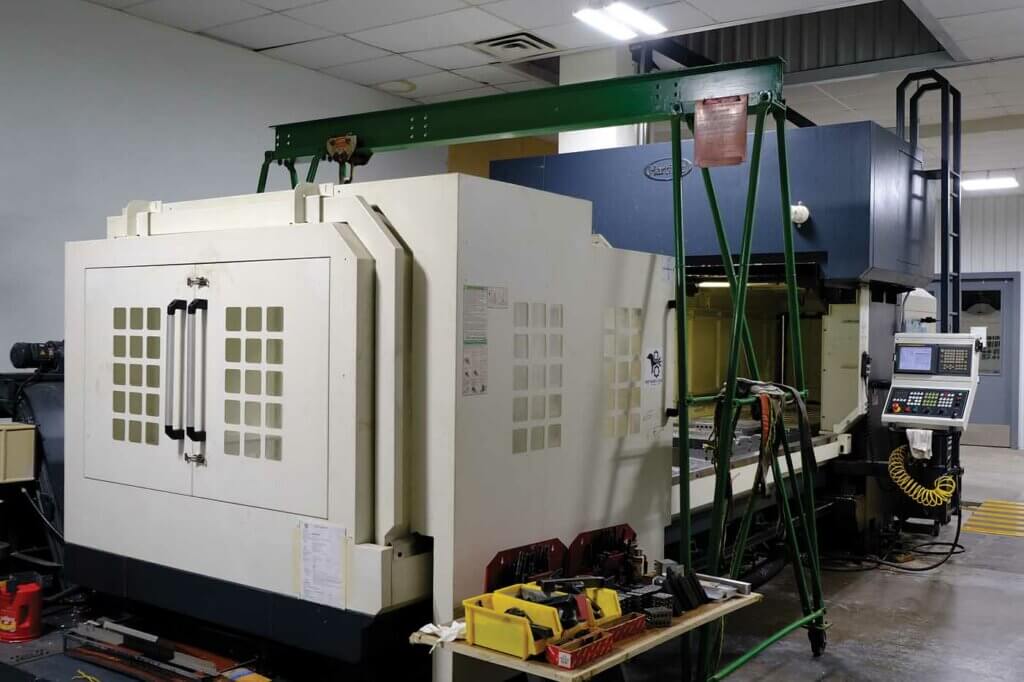
In addition, and to better serve its customers, the IAC team has recently obtained AS9110 and AS9100 certifications.
“We are very proud of these distinctions as we continue to reach new goals,” said director of sales and marketing Alfredo Garza.
The IAC 53,450-square-foot (4,965-square-meter) facility is located in Fort Worth, Texas. It includes a composite material cutting room, controlled environment cleanroom, static balance room, engineering lab, integrated machine shop, and extensive testing capabilities. Since 1992, IAC has honed its skills and processes to ensure the efficient and safe inspection and repair of both metal and composite blades.
IAC is a part 145 repair station certified by the U.S. Federal Aviation Administration (FAA) and the European Union Aviation Safety Agency (EASA). As part of the Fort Worth aviation cluster — with helicopter manufacturers including Sikorsky, Bell, Schweizer, and Airbus — IAC can draw from a pool of experienced technicians, but the company is always looking to expand its staff with new talent to strengthen its capabilities.
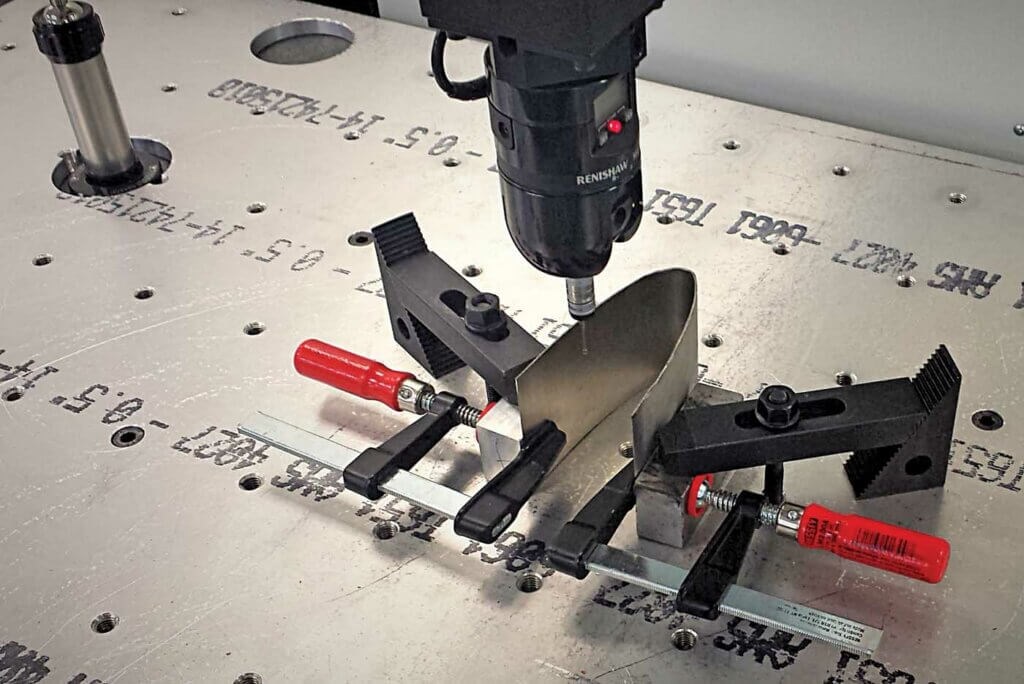
“We like to utilize skills from other industries as well, including our military veterans,” said Kenny Murray, IAC’s production manager. “It makes it easier to train our technicians, and it does take a couple of years to properly train someone to perform blade repairs.”
When a blade comes to IAC for repair, the inspection department can draw on its extensive data history and determine if it has an approved repair process on file.
IAC president Randy Stevens said the company’s in-house engineering capability gives the company the ability to develop new repair processes, which are sent to the FAA for approval before the work is done.
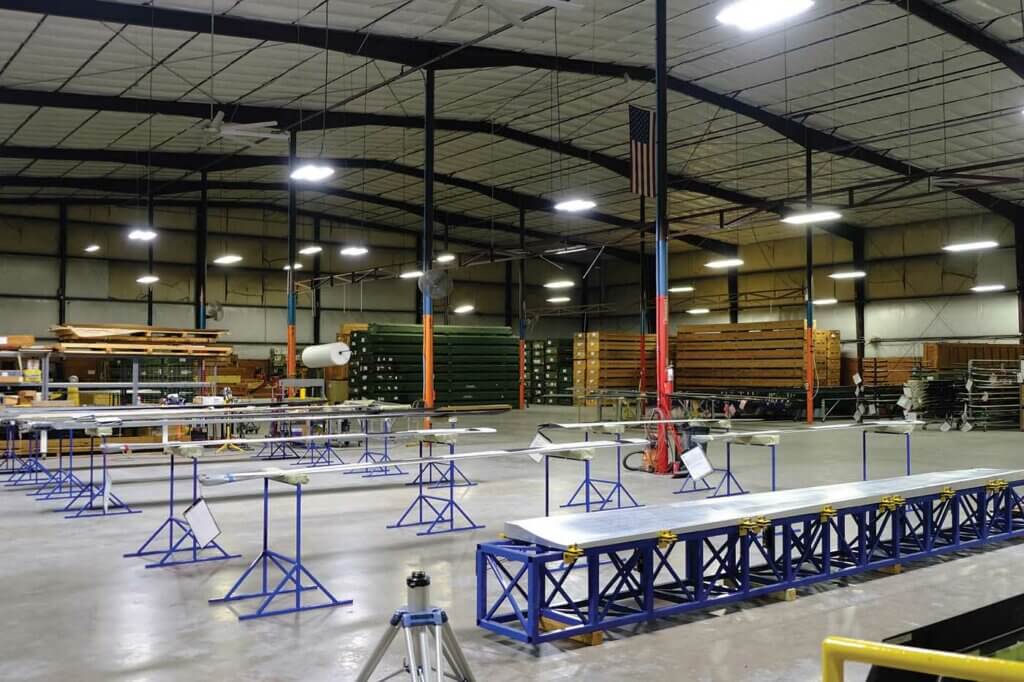
“There are two types of FAA approval for repair data. One is a serial number specific repair, which is tied to a blade with a specific serial number or a series of serial numbers. There are also repair specifications, which are tied only to a blade part number, so the specification is available for repetitive use,” Stevens said. “We do not have to depend on OEMs [original equipment manufacturers] for repair data. We have the ability to develop our own through reverse engineering and materials testing, as required.”
As rotor blade design and manufacturing technology have advanced and evolved, IAC’s repair processes have stayed in step.
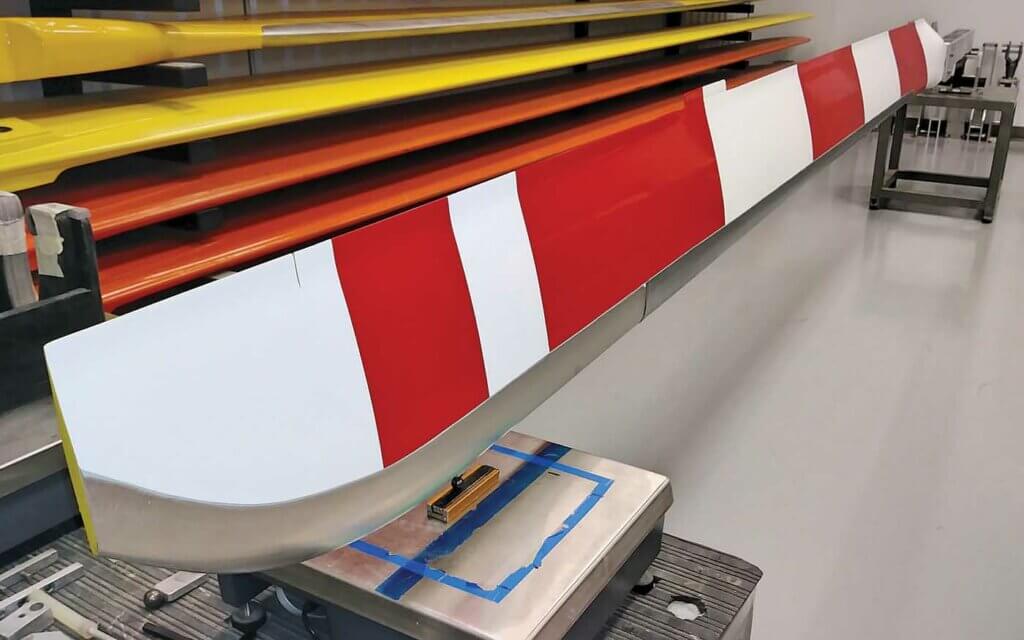
Blade repairs were once done with discrete tools, with a specific tool required for each blade or each type of repair.
To improve the process, IAC developed a universal autoclave tool that enables its technicians to make large repairs on virtually any kind of rotor blade. To properly cure the repair of a composite blade, it needs time in an autoclave under pressure and high temperature.
The interior of IAC’s autoclave is equipped with a bank of electrical outlets, so while the unit is pressurized, the interior air isn’t heated — instead, the rotor blades get a direct heat treatment.
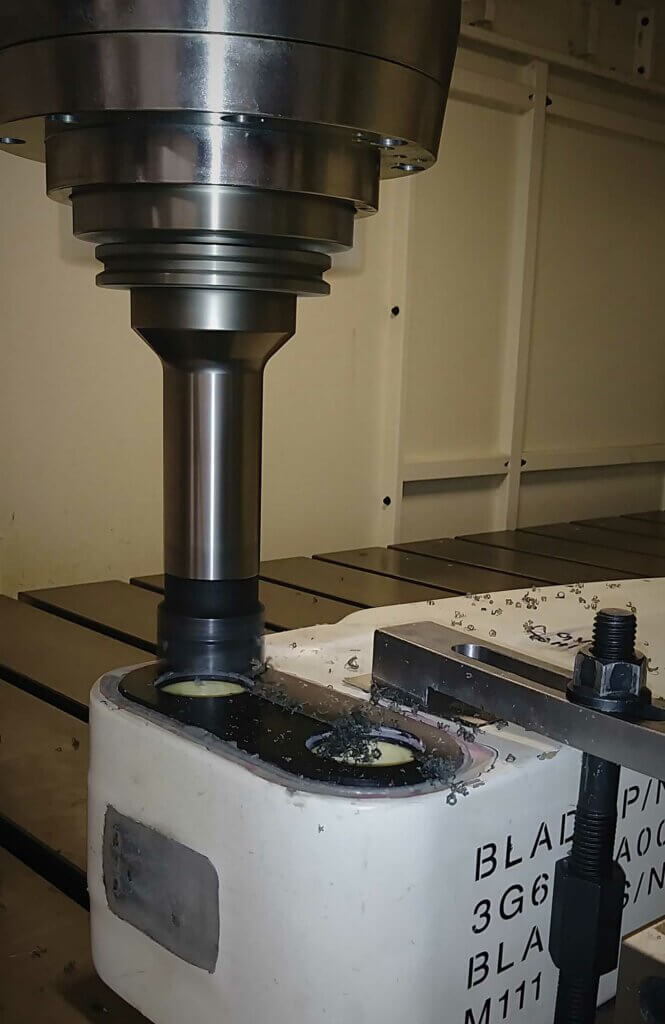
“We use electric heat blankets. You get the pressure of an autoclave, but it gives you the localized heating capability of a heat blanket. The repairs are more even, with improved pressure uniformity,” Stevens said.
Overall, the average repair interval on composite blades is much longer than on metal blades, and the development of composite blades has led to a significant reduction in the need for rotor blade maintenance, along with improved repair techniques.
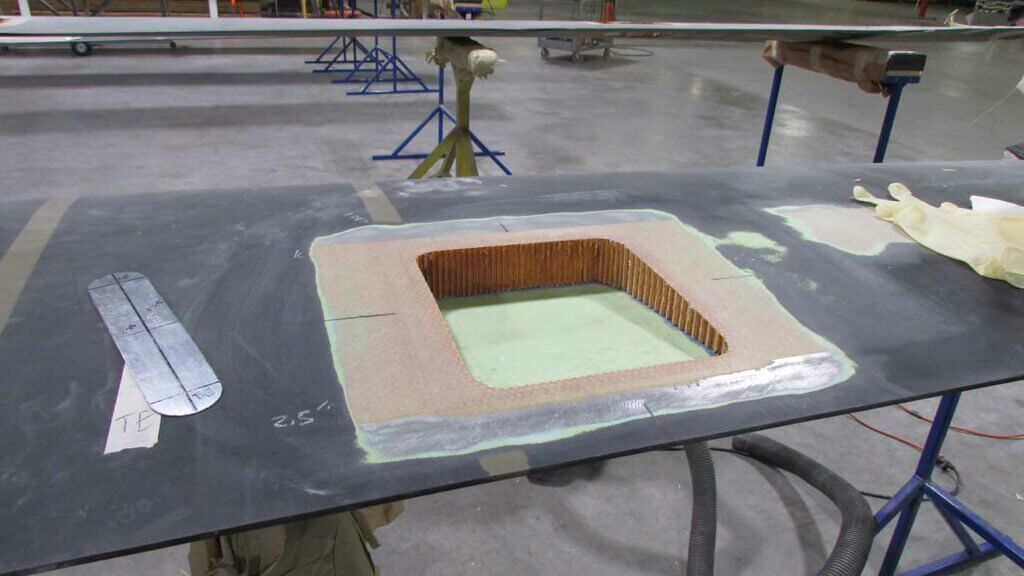
“It’s not too often that we can’t repair a blade,” Murray said. “It really has to be in quite bad shape before we determine that it is scrap.”
And if a blade can’t be repaired, he said that IAC is maintaining its policy of not charging its customers for the cost of the inspection.
“We’ll have to give them the bad news, but not a bill. That in itself is good for a customer,” he said.

With IAC’s success rate in repairs, Stevens points to that overall benefit to his customers.
“It’s the innovations that we’ve been able to make in blade repair, and the blades we’ve been able to save for customers, especially for the smaller operators. If they have to go buy a new rotor blade, it just crushes their budget,” he said.
Along with its solid reputation for quality work, it’s the helicopter industry’s personal network on which IAC relies to reach new customers.
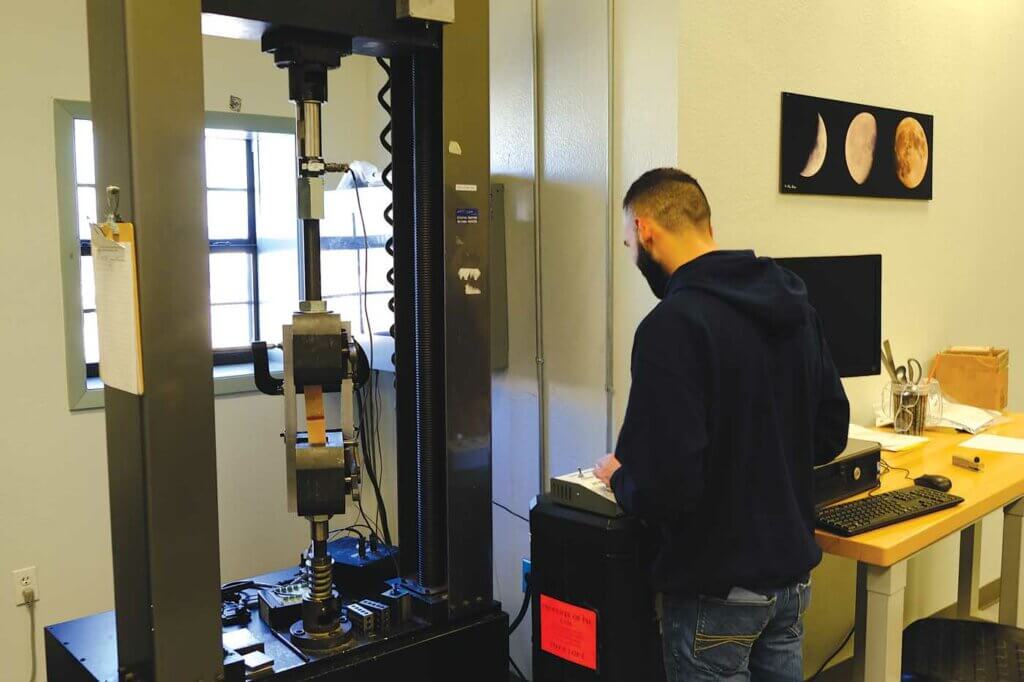
“Many of our new customers come to us primarily word-of-mouth. That has been very successful for us over the last 30-plus years,” Stevens said.
“IAC is big enough to handle all repair needs, but small enough to provide personal service to our customers,” Murray added. “Our outstanding customer support team is always available, including after hours support if needed, and we treat each customer the same, whether they need just one blade inspected or a set of blades repaired. Our company-wide commitment to providing quality service at a reasonable cost and quick turnaround time is paramount for IAC’s continued growth and success.”