Fifteen hundred — that’s the number of U.S. manufacturers already in a database that can be accessed by eVTOL makers for components, airframes, and entire systems as they prepare for mass production and market launch.
These 1,500 are a small but mighty number of the 170,000 companies in the CONNEX Marketplace, a database that connects new and established U.S. businesses, government contractors and more with manufacturers to get their products made.
The entire database is categorized based on manufacturing capability, for example, injection molding and various types of machining, as well as finished materials, certifications and more — and it’s open to all sectors.
According to Alan Davis, CEO of i5, which created the CONNEX Marketplace, this matters a lot in light of the upcoming manufacture of eVTOLs.
“For decades, there have been siloed organizations of manufacturing in defense, aerospace, automotive, and many other subsectors,” he said. “That means that each subsector had a pool of manufacturers they called on and didn’t often look outside it. [Meanwhile], there are many other companies that could provide the component or systems required. Those siloes have stymied opportunities for U.S. companies, slowed down timelines and made manufacturers more vulnerable to individual sector disruption. It’s better for everyone to have a wide net. We hope that manufacturing of eVTOLs will play out this way and be different in several other important ways as well.”
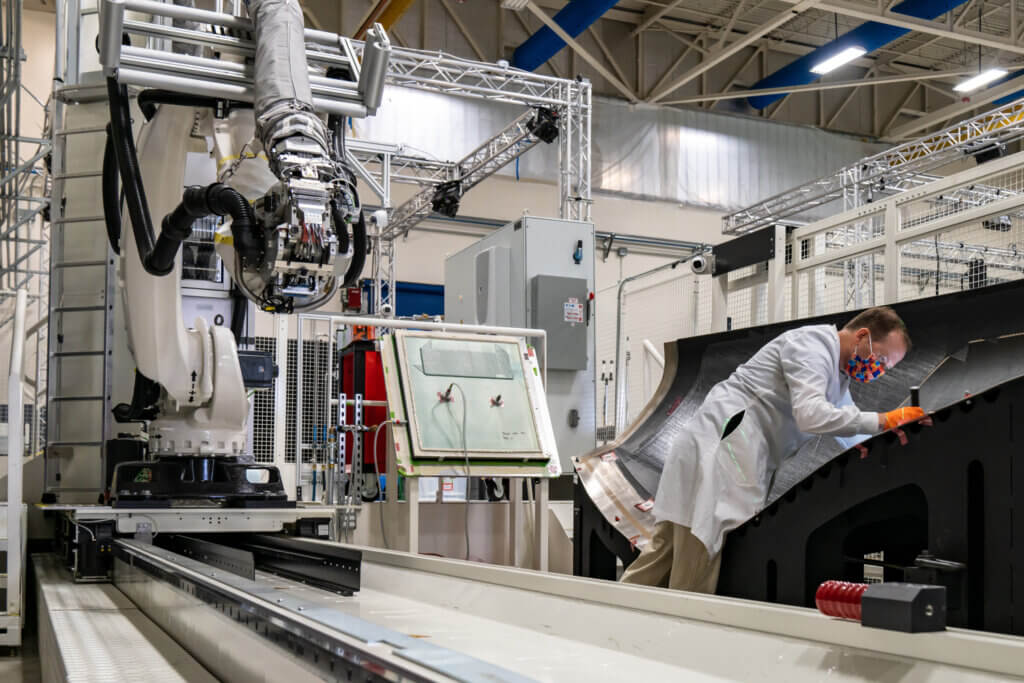
A look at CONNEX
It was over a decade ago in 2013 when Davis and his team were approached by the Utah state government to build a database of local manufacturers based on capabilities. And in 2015, the National Association of Manufacturers approached them to build a national version.
“We officially partnered in 2017, rolled out the beta version the year after, then kicked off in 2019,” Davis explained. “Around that time, Vertical Flight Society [VFS] approached us to help them with building a manufacturing ecosystem for eVTOLs — for the aircraft, charging, vertiports, all of it. The 1,500 companies were selected by us, VFS and the other development partner NEXA because they’re specifically suited to help with making eVTOLs, but of course, eVTOL companies can search and connect with any manufacturer in CONNEX with the needed capability.”
But what else should be different in eVTOL manufacture, besides being able to easily find the component or systems manufacturer with the right capabilities? And what other inefficiencies or problems from the previous decades of manufacturing in other sectors can and should be sidestepped in making eVTOLs?
Davis has answers.
The eVTOL supply chain
Concerning the attributes the eVTOL supply chain should have in order to best serve the industry, Davis first pointed to what must be avoided.
“In automotive and other sectors, we’ve had just-in-time manufacturing, with the actual assembly lines being very efficient and providing excellent quality control,” he said. “It worked well with the supply chains that existed. But we’ve seen during the pandemic that supply chains broke down at many points. There are various reasons for that and they’re hard to change. So what else can we do?”
“Well, we can stockpile, but that is not a good strategy and has numerous deficiencies. Just-in-time is already changing and needs to be done differently, so let’s improve it with making eVTOLs and their chargers.”
Davis proposed making parts much closer to the plant, and perhaps even making many parts inside the plant itself.
“It sounds like a no-brainer at this point, with the pandemic in the rearview mirror, but it really isn’t an idea that’s gotten much traction in the past. But if you do this with eVTOLs, you will eliminate a lot of supply chain vulnerability, you remove choke points, and you’ll have much more efficiency than what we still see in supply chains in other sectors like automotive today.”
This is achievable with eVTOLs, Davis said, with one exception: a majority of the world’s computer chips are basically made in Asia.
“The day will come when they’re made here, but probably not before eVTOLs hit the assembly line,” he said. “But that shouldn’t stop us with every other component. We are still early enough in this industry to do things differently — and the eVTOL sector should be looking to adopt new sources of supply for chips, to be ready to switch to that.”
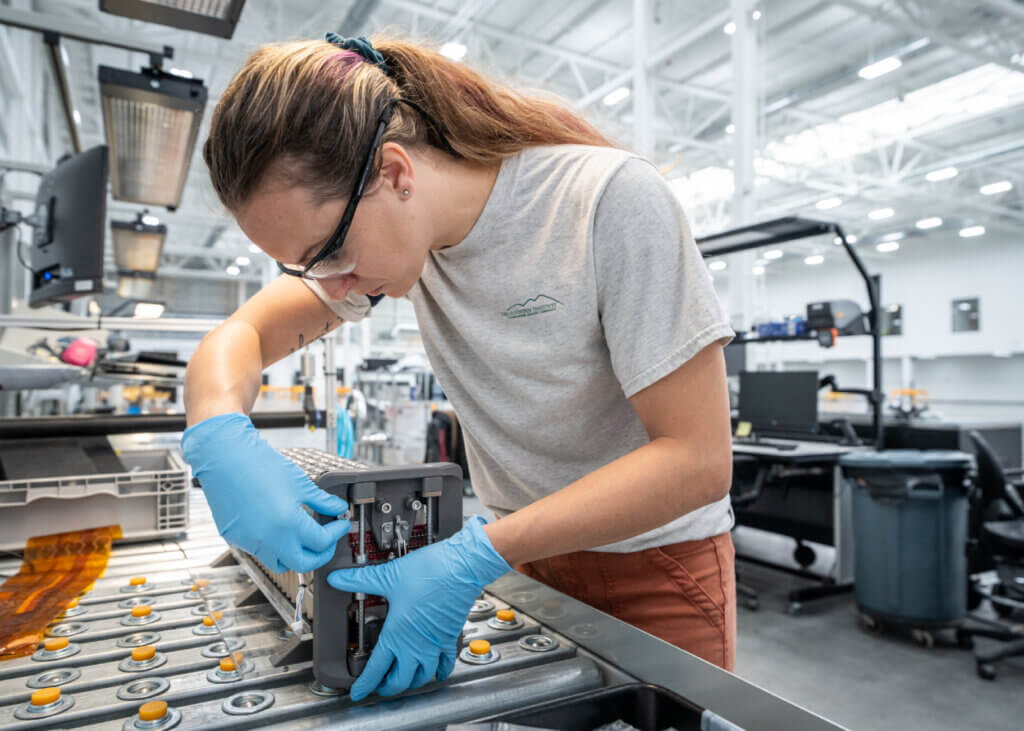
Location and collaboration
Davis also mused that eVTOL manufacturing should be closest to the largest demand hubs — New York, Miami, Los Angeles, and Las Vegas — but other factors, such as workforce availability and location of manufacturing partners, have caused many eVTOL firms to situate future large-scale manufacture elsewhere. On the other hand, Jaunt Air Mobility Canada, based in Quebec, signed an agreement last year with supply chain service provider Global Partner Solutions to establish a supply chain ecosystem with a focus on engaging Quebec-based suppliers.
Davis would also like to see more companies working together to use common components, which would enable greater sector-wide manufacturing efficiencies.
“I would have said prior to the pandemic there was little chance these things would even be considered, but company leaders have lived through the problems and there is a great desire to do things differently — to collaborate, to create our supply chains deliberately rather than allowing them to come to us,” he said.
Much collaboration is already happening in the eVTOL sector. Davis pointed to the Federal Aviation Administration and original equipment manufacturers (OEMs) working together in testing activities, certification discussions and more at the Daisy Ranch site in Oklahoma.
Beta Technologies has created an interoperable and multimodal fast-charging system for any eVTOL, and Archer Aviation has purchased several of these units as part of a new partnership. Going beyond collaboration, Joby Aviation has created a universal quick charging interface and the specifications will be freely available.
Manufacturing collaborations
Although Beta Technologies is going it alone with its eVTOL manufacturing located in Vermont, several major eVTOL firms have announced manufacturing partnerships with aviation firms.
China-based EHang is working with Monarch Airplane Manufacturing to establish an eVTOL plant in the Middle East/Africa, in Abu Dhabi. Lift Aircraft has partnered with Texas-based Qarbon Aerospace, which currently manufactures the Hexa’s carbon fiber structure at its Thailand facility, with the full integration of the aircraft occuring in Red Oak, Texas.
Other eVTOL firms have formed automaker manufacturing partnerships, including Supernal and Hyundai, SkyDrive and Suzuki and Archer and Stellantis. Archer is building a plant in Georgia, which it said will be able to produce 650 of its eVTOL aircraft a year by the second half of 2024.
Eve Air Mobility is partnering with Porsche Consulting to define Eve’s eVTOL global manufacturing, supply chain and logistics macro strategy. Its first eVTOL plant will be located in Brazil.
Joby Aviation is collaborating with Toyota, a long-term investor in the firm. Toyota worked with Joby on the design and launch of Joby’s pilot production line in Marina, California, and plans to continue to advise Joby as it prepares for scaled production of its commercial passenger air taxi in Ohio.
Joby plans to build a facility, which it claims will be capable of making up to 500 aircraft per year at the Dayton International Airport in Ohio. Construction is expected to start this year and production in 2025.
The “existing talented workforce in the area” played an important role in site selection, said Joby spokesperson Katie Pribyl.
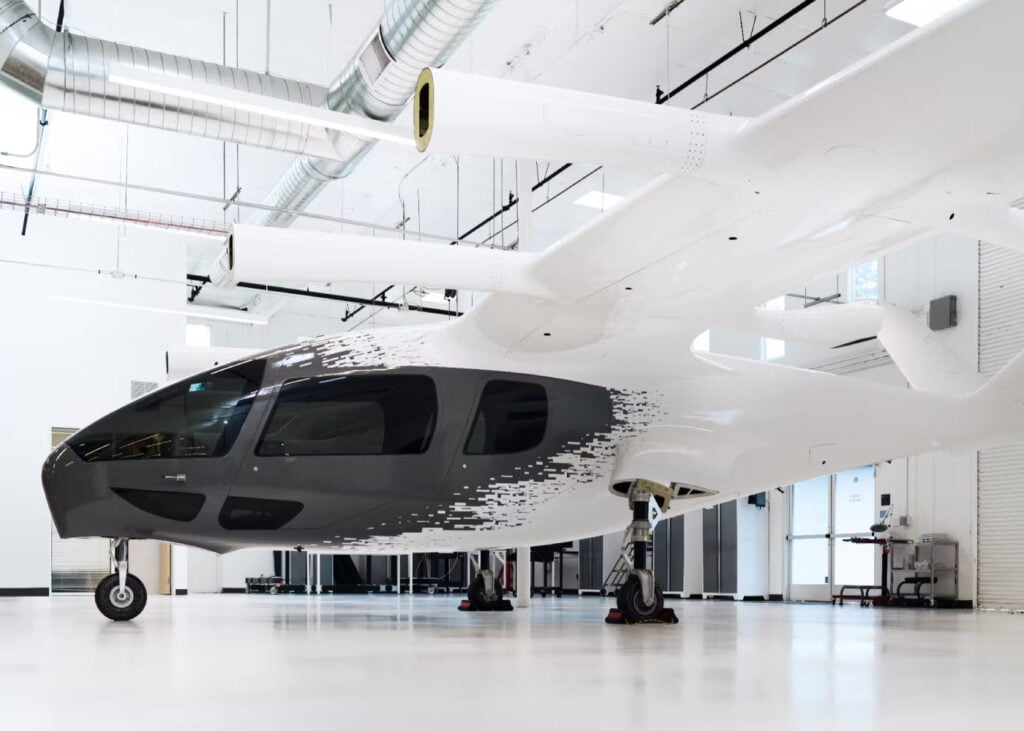
Why automotive?
It’s not hard to understand why Joby and other eVTOL firms are partnering with automotive firms on manufacturing.
For Joby, Pribyl explained that as the world’s largest automaker, “Toyota is known worldwide for the quality and reliability of its vehicles. Toyota’s expertise is invaluable for us as we plan to manufacture aircraft at scale and, together, we’ve completed dozens of projects related to the production and assembly of our aircraft, from consulting on the layout of our pilot production facilities to solving individual manufacturing challenges across various aircraft systems. Toyota excels at efficient scale manufacturing and production quality, and we are very happy to be working with them on the design of our future factory in Dayton, Ohio, as well as continued improvements at our Marina and San Carlos facilities.”
Pribyl also noted that Joby, as a vertically-integrated manufacturer, “has more control over our supply chain than companies taking the approach of a traditional integrator. We believe this approach has not only allowed us to design a more performant aircraft, but also grants us more control of our manufacturing and certification timelines, costs and quality controls.”
When asked about collaborations with automakers, Davis stressed again that the sector should learn from its past and do things differently going forward.
“There is so much to learn from the automotive industry and others and that affords us insights into ways in which we can do things better from the start of mass eVTOL production,” he said. “There are efficiencies and improvements to be realized by examining everything from the intentional ways that manufacturing has been set up in China to the ways in which we have responded and adapted to supply chain disruptions during the pandemic.”
Going forward, he said, “we can be more intentional.”